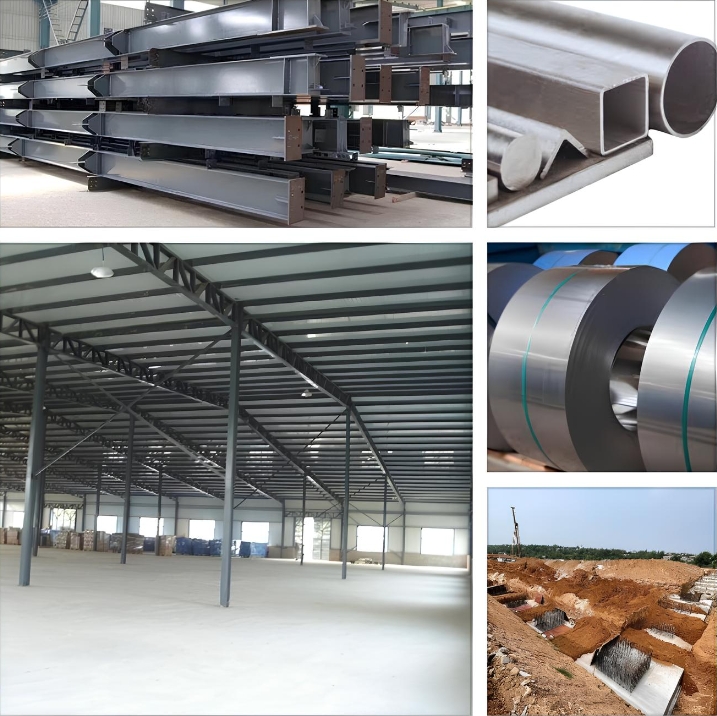
The growing popularity of steel buildings across industrial, agricultural, and commercial applications is no coincidence. These structures offer a combination of structural integrity, adaptability, and construction efficiency. Yet, beneath their functional appeal lies a complex web of cost determinants that can significantly influence the total project expenditure. Understanding these variables is essential for accurate budgeting and value-driven decision-making.
1. Size and Spatial Configuration
The dimensions of a steel building are foundational to its cost, but this extends beyond simple square footage. Larger structures typically benefit from economies of scale, resulting in a lower unit cost per square meter. However, expansive clear spans, tall eave heights, and multi-level designs necessitate additional steel, heavier load-bearing components, and advanced engineering, all of which elevate structural complexity and cost. Non-rectangular layouts or designs incorporating mezzanines also demand more intricate detailing and custom fabrication.
2. Steel Grade and Treatment
Material selection exerts a direct influence on both performance and price. High-strength, low-alloy structural steels enhance structural capacity but come at a premium. Additionally, corrosion protection methods—such as galvanization, powder coatings, or fire-resistant finishes—extend durability yet increase upfront material costs. Market fluctuations in steel pricing, often tied to geopolitical tensions or supply chain constraints, further complicate procurement. Early procurement strategies may mitigate cost volatility.
3. Architectural and Functional Complexity
Simple, utilitarian designs remain the most economical. However, buildings tailored for specific operational needs—like those requiring overhead cranes which need crane beams, extensive natural lighting, or complex facades—entail higher engineering and fabrication demands. Every custom element, from skylights to curtain walls, adds to the structural and installation workload, affecting not only costs but also timelines.
4. Site-Specific Challenges
The characteristics of the construction site often impose hidden expenses. Irregular terrain may necessitate extensive grading, while unstable soil conditions require robust foundations to ensure stability. Remote or congested sites complicate logistics, resulting in increased costs for transportation, labor coordination, and equipment deployment. Moreover, regional differences in labor rates and material availability further shape the final budget.
5. Groundwork and Foundation Systems
Site preparation is a foundational but frequently underestimated expense. Before structural erection, the land must be cleared, leveled, and compacted, potentially requiring environmental approvals or local permits. The foundation system itself varies according to ground conditions and structural loads. While a slab-on-grade is economical, poor soils may require deep foundations or reinforced footings, which can significantly increase driving costs.
6. Construction Labor and Methods
Labor expenditures hinge on local availability, skill level, and construction methodology. Pre-engineered systems enable rapid assembly, resulting in reduced person-hours and associated costs. In contrast, site-intensive builds with complex detailing may necessitate specialized labor and longer timelines. Project delays, whether caused weather or change orders, further exacerbate labor and equipment rental costs.
7. Internal Systems and Finishes
Beyond the steel frame lies a multitude of essential installations—electrical, plumbing, HVAC, and fire safety systems—all requiring coordination and expertise. Buildings intended for frequent occupancy or specialized operations require additional insulation, energy-efficient envelopes, and interior partitions, which substantially impact the cost depending on the quality and performance standards.
Conclusion
A constellation of interrelated elements shapes the steel buildings. From design specifications to site logistics, each factor contributes not only to the initial capital outlay but also to the building’s long-term performance and value. Precision in planning, transparency with vendors, and flexibility in response to emerging challenges are key to achieving a cost-effective and high-performing steel building solution.